分享:S32101双相不锈钢焊接接头晶间腐蚀试验不合格原因
唐琴燕,黄敏敏,许云伟,刘恒基,叶尚杰,姜思源
(中国能源建设集团浙江火电建设有限公司,杭州 310016)
摘 要:为探究S32101双相不锈钢焊接后接头晶间腐蚀试验不合格的原因,对晶间腐蚀试验不合格的焊接接头进行了金相检验、X射线光电子能谱(XPS)分析和铁素体含量测试。结果表明:晶间腐蚀试验不合格的原因是材料存在化学成分偏析,造成铬的质量分数偏低,且焊接过程中在晶界处析出碳化铬,形成贫铬区,导致材料的抗晶间腐蚀能力降低。另外,显微组织中的铁素体含量偏低,也增加了贫铬区形成的可能性,进一步降低了抗晶间腐蚀能力。
关键词:晶间腐蚀;金相检验;X射线光电子能谱分析;铁素体;贫铬区
中图分类号:TG17 文献标志码:A 文章编号:1001-4012(2021)05-0014-04
CauseofFailureinIntergranularCorrosionTestofS32101Duplex
StainlessSteelWeldedJoint
TANGQinyan,HUANG Minmin,XUYunwei,LIUHengji,YEShangjie,JIANGSiyuan
(ChinaEnergyEngineeringGroupZhejiangThermalPowerConstructionCo.,Ltd.,Hangzhou310016,China)
Abstract:InordertoexplorethereasonofunqualifiedintergranularcorrosiontestofS32101duplexstainless
steelweldedjoint,metallographicexamination,Xrayphotoelectronspectroscopy(XPS)analysisandferritecontent
testwerecarriedoutonweldedjointwhichfailedinintergranularcorrosiontest.Theresultsshowthatthereason
forthefailureofintergranularcorrosiontestisthatthereischemicalcompositionsegregationinthe material,
resultinginthelowcontentofchromium,andchromium carbideprecipitatesatthegrainboundaryduringthe
weldingprocess,formingachromiumpoorzone,whichleadstothereductionofintergranularcorrosionresistance
ofthematerial.Inaddition,thelowcontentofferriteinthemicrostructurealsoincreasesthepossibilityofthe
formationofchromiumpoorzoneandfurtherreducestheresistancetointergranularcorrosion.
Keywords:intergranularcorrosion;metallographicexamination;X-rayphotoelectronspectroscopyanalysis;
ferrite;chromiumpoorzone
核能 发 电(简 称 核 电)作 为 一 种 安 全、高 效 的清洁能源,在 全 球 范 围 内 被 广 泛 应 用。据 国 际 原子能机构(IAEA)统计,到2019年6月底,全球共有449台核电 机 组 在 运 行,分 布 在 30 个 国 家,核电发电容量近4亿 kW,另有54台核电机组在建,发电容 量 约 为 5500万kW。我 国 大 陆 运 行 核 电机组共47台,发电容量4873万kW;在建机组11台,发电 容 量 约 1134万kW,多 年 来 保 持 全 球 首位[1]。在核 电 应 用 及 发 展 前 景 持 续 看 好 的 情 况下,核电安 全 也 引 起 全 球 的 重 视。
在 核 电 站 建 设 中,对其结构材料的要求非常严苛,其中一项就是 要求材料具有优异的耐腐蚀性能。双相不锈钢凭 借其优异的 力 学 性 能、耐 腐 蚀 性 能 和 焊 接 性 能 在 第三代核电机组中被广泛应用。在非能动先进压 水堆 AP1000核 电 站,S32101 双 相 不 锈 钢 被 用 于 换料通道、乏 燃 料 水 池、换 料 水 池、反 应 堆 腔 室 等 位置。对于在建非能动先进压水堆 AP1400核电 站,S32101双相不锈钢也被用于辅助厂房6区的 钢板混凝土 模 块、蒸 汽 发 生 器 隔 间 和 换 料 通 道 模 块、内置换料水箱模块、化学和容积控制系统的强 模块等结构模块的安装中。
与铁素体不锈钢相比,S32101双相不锈钢的塑性、韧性更高,无室温脆性,耐晶间腐蚀性能和焊接性能均较高,同时还具有铁素体不锈钢的475 ℃脆性、导热系数高及具有超塑性等特点;与奥氏体不锈钢相比,S32101双相不锈钢的强度高且耐晶间腐蚀和耐氯化物应力腐蚀性能明显提高。但 S32101双相不锈钢在氧化和弱氧化介质中容易发生晶间腐蚀,晶间腐蚀是从表面沿晶界向内部延伸的,会使材料的强度严重降低,导致材料受到较小的外力就会沿晶界断裂,而表面却完好、光亮,所以晶间腐蚀是一种具有极大危险性的破坏,因此要求材料必须具有足够的抗晶间腐蚀能力。某工厂为保证产品质量,必须对经施焊的构件进行焊接接头晶间腐蚀试验[2]。但是在一次 S32101钢的焊接工艺评定中发现,焊缝区有裂纹缺陷,即焊接接头的晶间腐蚀试验不合格,为找到焊接接头晶间腐蚀试验的不合格原因,笔者进行了一系列分析。
1 晶间腐蚀机理
不锈钢在腐蚀介质中,其晶粒之间发生的一种腐蚀现象称为晶间腐蚀,晶间腐蚀机理如图1所示。晶间腐蚀可以发生在焊接接头的热影响区、焊缝或熔合线等位置,其中在熔合线上发生的晶间腐蚀又称刀 线 腐 蚀。 有 试 验 表 明,铬 的 质 量 分 数 大 于10%~12%时不锈钢才会具有耐腐蚀能力[3]。介质中,贫 铬 区 会 失 去 耐 腐 蚀 能 力 而 发 生 晶 间 腐蚀[6]。
2 晶间腐蚀试验
采用合格的材料、设备和合理的工艺进行焊接,接头经过射线检测合格后,根据ISO3651-1:1998Determination of resistance to intergranularcorrosion of stainlesssteelsPart1:Austeniticandferritic-austenitic(duplex)stainlesssteels—Corrosion test in nitric acid mediumbymeasurementoflossinmass(Hueytest)的技术要求对焊接接头进行晶间腐蚀试验,试验过程如下。
(1)敏化热处理,将试样加热到(700±10)℃后保温30min,然后水冷。
(2)试样表面处理,用砂纸去除试样表面的氧化皮,并进行去油处理。
(3)配 制 腐 蚀 液,在 700 mL 蒸 馏 水 中 溶 解100g五水硫酸铜(CuSO4·5H2O),加入100mL硫酸(密度ρ为1.84g·mL-1),然后加水至溶液达到1000mL。
(4)腐蚀试验,将处理好的试样嵌入烧瓶底部的电工级铜屑中,试样应与铜屑接触,但试样之间互相不接触。首先把试样浸入冷的腐蚀液中,然后将溶液加热到沸腾,并使腐蚀液保持沸腾20h。
(5)弯曲试验,腐蚀试验完成后,在一个半径不超过试样厚度的芯棒上对试样进行至少90°的弯曲试验。晶间腐蚀试验结果如图2所示,可见焊缝处有裂纹缺陷。
2 晶间腐蚀试验
采用合格的材料、设备和合理的工艺进行焊接,接头经过射线检测合格后,根据ISO3651-1:1998Determination of resistance to intergranularcorrosion of stainlesssteelsPart1:Austeniticandferritic-austenitic(duplex)stainlesssteels—Corrosion test in nitric acid medium bymeasurementoflossinmass(Hueytest)的技术要求对焊接接头进行晶间腐蚀试验,试验过程如下。
(1)敏化热处理,将试样加热到(700±10)℃后保温30min,然后水冷。
(2)试样表面处理,用砂纸去除试样表面的氧化皮,并进行去油处理。
(3)配 制 腐 蚀 液,在 700 mL 蒸 馏 水 中 溶 解100g五水硫酸铜(CuSO4·5H2O),加入100mL硫酸(密度ρ为1.84g·mL-1),然后加水至溶液达到1000mL。
(4)腐蚀试验,将处理好的试样嵌入烧瓶底部的电工级铜屑中,试样应与铜屑接触,但试样之间互相不接触。首先把试样浸入冷的腐蚀液中,然后将溶液加热到沸腾,并使腐蚀液保持沸腾20h。
(5)弯曲试验,腐蚀试验完成后,在一个半径不超过试样厚度的芯棒上对试样进行至少90°的弯曲试验。
晶间腐蚀试验结果如图2所示,可见焊缝处有裂纹缺陷。
3 结果及分析
3.1 微观形貌
对图2中区域2焊缝裂纹区表面打磨、抛光后,在光学显微镜下进行观察,其微观形貌如图3所示。可见裂纹沿晶界扩展,裂纹附近存在圆形腐蚀坑。因此判断该裂纹属于晶间腐蚀产生的裂纹,裂纹附近有圆形腐蚀坑,说明焊接过程中,在敏感温度区停留时间过长,造成碳化物析出。
可见裂纹沿晶界扩展,裂纹附近存在圆形腐蚀坑。因此判断该裂纹属于晶间腐蚀产生的裂纹,裂纹附近有圆形腐蚀坑,说明焊接过程中,在敏感温度区停留时间过长,造成碳化物析出。
3.2 金相检验
在图2中区域2焊缝裂纹区截取金相试样,打磨、抛光后,对试样表面浸蚀,然后在光学显微镜下进行观察,显微组织形貌如图4所示,可见显微组织为奥氏体+铁素体(黑色凹坑处为铁素体),晶粒与晶粒之间呈沟槽状。
3.3 X射线光电子能谱分析
X 射线光电子能谱(XPS)是一种基 于 光 电 效应的电子能谱,其是利用 X 射线光子激发出物质表面原子的内层电 子,然 后 通 过 对 这 种 电 子 进 行能量分析而获得 的 一 种 电 子 能 谱[7-9]。 对 图 2 中的区域 1 与 区 域 2 分 别 进 行 XPS分 析,结 果 如图5和图 6 所 示,横 坐 标 表 示 的 是 电 子 束 缚 能(能直接 反 映 电 子 壳 层、能 级 结 构 或 动 能),纵 坐标表示相对光 电 子 流 强 度,可 见 区 域 1 与 区 域 2均含有钠、铁、铬、氧、氮、碳 和 氯 元 素。去 掉 图 5和图6 中 非 相 关 元 素 之 后,得 到 的 有 效 数 据 如表1所示。
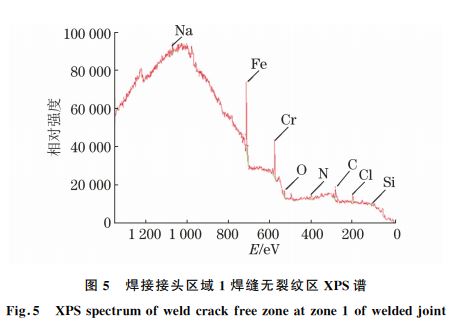
由表1可知,出现裂纹的区域2在焊接过程中产生了化学成分偏析,造成区域2铬质量分数降低,远未达到焊材质保书中21.5%~23.5%的要求,致使该处抗晶间腐蚀能力减弱。电化学从本质上来说,是材料中各物质在腐蚀介质中的溶解速率不同,从而产生电极电位差,形成阴、阳两极,会进一步导致阳极的加速溶解[10]。铬元素会在材料表面形成一层致密的钝化膜,降低阳极的溶解速率,而晶界处贫铬区的铬钝化膜不完整,最先被腐蚀,从而导致晶间腐蚀。
3.4 铁素体含量测试
用磁性法[11]对试样的焊缝区域1和区域2进行铁素体含量测试,结果如表2所示。可见裂纹所在区域(区域2)的铁素体含量过低,则奥氏体含量高,奥氏体在碳化铬析出时,更多的铬留在了奥氏体晶粒内导致更容易形成贫铬区,进而增大发生晶间腐蚀的可能性。
4 结论
晶间腐蚀试验不合格的原因是材料存在化学成分偏析,造成铬的质量分数偏低,且焊接过程中在晶界处析出碳化铬,形成贫铬区,导致材料的抗晶间腐蚀能力降低。另外,显微组织中的铁素体含量偏低,也增加了贫铬区形成的可能性,进一步降低了抗晶间腐蚀能力。
5 改进措施
为提高核电站中双相不锈钢的抗晶间腐蚀能力,要严格控制焊接工艺,避免发生晶间偏析;缩短焊接过程中在敏化区的停留时间,抑制贫铬区的形成;控制铁素体的含量,不能过低亦不能过高。