分享:00MW 超临界电站锅炉末级过热器管爆裂失效分析
600MW 超临界电站锅炉末级过热器管爆裂失效分析
晏嘉陵
(中国大唐集团 科学技术研究院有限公司 华东分公司,合肥 230088)
摘 要:通过宏观检验、室温拉伸试验、金相检验、硬度试验等方法对某600 MW 超临界电站锅炉末级过热器管发生爆裂的原因进行了分析.结果表明:该爆裂管经历过长期超温运行,组织老化严重,产生蠕变孔洞并连接形成裂纹,最终导致其在最薄弱的弯头外弧面处发生爆裂.
关键词:末级过热器;爆裂;失效分析;长期超温;组织老化;蠕变孔洞
中图分类号:TK223.3;TG115 文献标志码:B 文章编号:1001G4012(2017)06G0445G04
收稿日期:2017G02G28
作者简介:晏嘉陵(1984-),男,工程师,硕士,从事电站金属部
件监督及结构寿命评估工作,jialing_yan2009@163.com
FailureAnalysisonBurstingoftheFinalGStageSuperheaterTube
ina600MW UltraGSupercriticalBoiler
YANJialing
(EastChinaBranch,ScienceandTechnologyResearchInstituteCo.,Ltd.,ChinaDatangCorporation,Hefei230088,China)
Abstract:TheburstingfailurereasonsofthefinalGstagesuperheatertubeina600 MW ultrasupercriticalboilerwereanalyzedthroughthemethodsofmacroinspection,tensiletestatroomtemperature,metallographic
examination,hardnesstest,etc.TheresultsshowthattheburstingtubeexperiencedlongGtermoverheating,the
microstructurewasseriouslyaged,andcreepholesformedandconnectedtocracks,whichfinallyresultedinthe
burstingattheweakestpositionoftheelbowoutsidearcsurface.
Keywords:finalGstagesuperheater;bursting;failureanalysis;longGterm overheating;structureaging;
creephole
锅炉4管(过热器管、再热器管、水冷壁管和省煤器管)是电站锅炉的主要承压和受热部件.据粗略统计,锅炉4管事故约占国内锅炉事故的2/3,是影响火电机组安全经济运行的最主要因素之一[1G7].随着我国火电机组容量的不断提高,汽水系统的压力和温度也相应增加,在运行过程中出现了诸多问题.某电厂锅炉末级过热器管发生爆管事故,爆裂过热器管材料为 GB5310-2008«高 压 锅 炉 炉 用 无 缝 钢 管»中 的10Cr9Mo1VNbN(美 国 牌 号 T91)钢 管,规 格 为
?38.1mm×7.96mm;爆 裂 位 置 为 由 西 向 东 数 第28排、由外向内数第6根;过热器管累计运行时间约6×104 h.该锅炉型号为 SGG1918/25.4GM968,为超临界参数变压运行螺旋管圈直流、单炉膛、一次中间再热、单炉膛四角切圆燃烧方式、平衡通风、固态排渣、全钢构架、全悬吊结构、露天布置、Π型燃煤锅炉.过热蒸汽出口设计压力为25.4 MPa,设计温度为571℃.笔者对爆裂末级过热器管进行了检验和分析,查明了其爆裂原因,并给出了改进建议.
1 理化检验
1.1 宏观检验
爆裂末级过热器管爆口宏观形貌如图1所示,爆口位于钢管弯头背弧面,附近无明显胀粗,爆口沿钢管轴向长约30 mm.由于爆管后与其他过热器管相互吹损,爆口边缘部分位置吹损缺失,爆口附近部分未被吹损位置有明显龟裂纹.
1.2 室温拉伸试验
在爆裂末级过热器管上取4个拉伸试样,使用CMT5105微机控制电子万能试验机进行室温拉伸试验,试验结果取4个试样的平均值,见表1.可见钢管的抗拉强度和屈服强度均不能满足 GB5310-2008对10CrMo1VNbN 钢管的技术要求.
1.3 金相检验
在爆裂末级过热器管爆口附近、爆口背面、距离爆口200mm 和500mm 的直管段位置分别截取金相试样.试 样 经 磨 制、抛 光 和 化 学 侵 蚀 后 在 CarlZeissAxioObserverA1m 型金相显微镜下进行显微组织试样的.
可见爆口边缘管内壁有厚约0.32mm 的氧化皮,外壁氧化皮脱落严重,部分位置留有厚约 0.13 mm 的氧化皮,显微组织晶粒细小,晶粒度在7级左右.爆口边缘晶粒变形严重,附近有大量的蠕变孔洞,显微组织为铁素体+碳化物,马氏体已经完全分解,碳化物呈块状分布在铁素体晶界位置.
图3为爆口背面试样的显微组织形貌,可见管内壁 有 厚 约 0.17 mm 的 氧 化 皮,外 壁 有 厚 约0.12mm 的氧化皮,显微 组 织 晶 粒 细 小,晶 粒 度 在7级左右.显微组织中大部分马氏体分解成铁素体+碳化物,部分碳化物在铁素体晶界位置聚集长大成块状,部分碳化物仍弥散分布在基体中.
图4为距离爆口200mm 处的显微组织形貌,可见管内壁有厚约0.20 mm 的氧化皮,外壁有厚约0.27mm 的氧化皮,显微组织晶粒细小,晶粒度在7级左右.显微组 织 中 马 氏 体 已 经 完 全 分 解 成铁素体+碳 化 物,部 分 碳 化 物 在 铁 素 体 晶 界 位 置聚集长大成 颗 粒 状,部 分 碳 化 物 仍 弥 散 分 布 在 基体中.
图5为距离爆口500mm 处的显微组织形貌,可见管内壁有厚约0.18mm 的氧化皮,外壁有厚约0.23mm 的氧化皮,显微组织晶粒细小,晶粒度在7级左右.显微组织中部分区域尚有马氏体位相,部分区域马氏体已经分解成铁素体+碳化物,细小的碳化物在铁素体晶界位置聚集,部分碳化物仍弥散分布在基体中.
1.4 1.硬度试验
利用 THBG3000MDX 型布氏硬度计在金相试进行布氏硬度试验,结果见表2.硬度检测结果显示,爆裂末级过热器管各个位置的硬度均低于 DL/T438-2016«火力发电厂金属技术监督规程»规定的下限值.
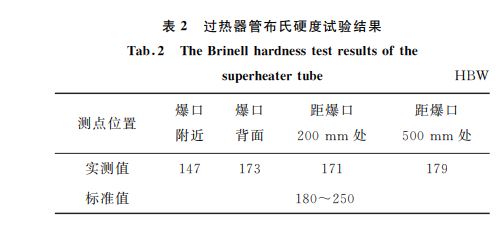
2 分析与讨论
由以上理化检验结果可知,爆裂末级过热器管的室温抗拉强度、屈服强度和硬度均低于标准规定的下限值,爆口附近显微组织中的马氏体完全分解为铁素体+碳化物,基体中的合金元素以碳化物的形式析出并在晶界位置聚集长大,爆口背面以及距离爆口200mm 和500mm 位置的显微组织也均有比较明显的老化趋势.在低于600 ℃运行时,T91钢中大量固溶的合金元素、弥散分布的碳化物和较高的位错密度使其具有良好的抗蒸汽氧化性能和长时持久强度.而在超过600 ℃的条件下长期运行时,T91钢中的合金元素会以碳化物的形式大量地析出、聚集和长大,显微组织中的马氏体加速分解,基体中的固溶强化、弥散强化和位错强化作用大大减弱,进而导致材料的持久强度快速下降.
3 结论
综合以上检验和分析可知,该超临界电站锅炉末级过热器管经历过长期超温运行,组织老化明显,材料持久强度显著下降.材料强度下降引起钢管发生蠕变胀粗,产生蠕变孔洞并连接形成裂纹,最终导致钢管在最薄弱的弯头外弧面处发生爆裂.
4 建议
(1)增加温度检测点,加强受热面钢管的温度监控,防止超温运行.
(2)扩大末级过热器管的割管检查范围,确定管材老化趋势,适时对末级过热器管开展服役安全性评价,确保锅炉安全稳定运行.
(3)定期检查弯头氧化皮堆积情况,防止因氧化皮堆积造成管内介质流量不足而导致局部超温.
更是在与螺母交界的螺纹根部产生了较大的单向应力集中.螺纹根部不断经受疲劳产生疲劳裂纹,疲劳裂纹不断扩展,当吊钩螺杆剩余截面不足以承重时便会发生最终断裂.
3 结论及建议
吊钩螺杆断裂属于应力集中造成的单向弯曲疲劳断裂;吊钩螺杆断裂的主要原因是长期的不当操作造成在断裂处产生较大的应力集中,在交变的弯曲应力作用下最终造成疲劳断裂.
鉴于以上分析,建议如下:①在起升货物的过程中,必须要缓慢起升货物,不能启动太快,避免产生冲击载荷;②经常检查吊钩各部位,检查和维护吊钩组的结构部件,如发现问题及时处理;③严格执行操作要求,避免不规范操作,尤其是起吊重物时应尽量避免横向撞击.
(文章来源: 材料与测试网-理化检验-物理分册 > 53卷 > 6期 (pp:445-448))