分享:航空复合材料-金属连接结构的拉伸性能及其渐进损伤
张浩宇1,侯 波2,何宇廷3,冯 宇3,谭翔飞3
(1.中国人民解放军95906部队,北京 102206;
2.陆军航空兵研究所,北京 101121;3.空军工程大学工程学院,西安 710038)
摘 要:利用有限元软件建立了某型飞机复合材料G金属连接结构件模型,以改进的 Camanho损伤退化模型作为失效判定准则,模拟了该连接结构件的拉伸性能和损伤累积过程并进行了试验验证.结果表明:在加装防弯夹具后,复合材料G金属连接结构件的拉伸试验结果更加准确,拉伸破坏模式由拉脱破坏变为挤压破坏;在较小的拉伸载荷下,其应变随载荷的增加呈线性增大,在金属上的应变明显大于复合材料层合板上的;损伤从复合材料和金属连接螺栓处产生,随载荷的增大逐渐累积并沿螺栓挤压方向扩展;模拟得到的最终破坏载荷为90kN,与试验值的相对误差仅为6.5%,证明了模拟结果的准确性.
关键词:复合材料;累积损伤;连接结构;失效准则;抗拉强度
中图分类号:V257 文献标志码:A 文章编号:1000G3738(2017)08G0087G06
TensilePropertyofAeronauticalCompositeGMetalJointStructureandItsProgressiveDamage
ZHANGHaoyu1,HOUBo2,HEYuting
3,FENGYu3,TANXiangfei3
(1.No.95906TroopsofPLA,Beijing102206,China;2.ArmyAviationResearchInstitute,Beijing101121,China;3.EngineeringCollege,AirForceEngineeringUniversity,Xi′an710038,China)
Abstract:ThemodelofthecompositeGmetaljointstructureofonetypeaircrafewasestablishedusingthe
finiteelementsoftware.Then withthe modifiedCamanhodamagedegradation modelasthecriterionoffailure
judgment,thetensilepropertyanddamageaccumulationprocessofthejointstructureweresimulatedandverified
bythetests.TheresultsshowthatafterassembledwiththeantiGbendingfixture,thetensiletestresultsofthe
compositeGmetaljointstructureweremoreaccurateandthetensiledamagemodechangedfrom pullGofffailuretocrushingfailure.Underrelativelylowtensileloads,thestrainincreasedlinearlywiththeincreaseofloadandwas
obviouslylargeronthemetalthanonthecompositelaminate.Thedamagewasproducedfromtheconnectingbolts
betweenthecompositeandmetal,thenaccumulatedgraduallyandextendedalongthecompressivedirectionoftheboltswiththeincreaseofload.Thesimulatedfinaldestructionloadwas90kNwiththerelativeerrorofonly6.5%comparingtothetestresult,indicatingtheaccuracyofthesimulation.
Keywords:composite;accumulateddamage;jointstructure;failurecriterion;tensilestrength
0 引 言
复合材料因具有比强度和比模量高、性能可设计和易于整体成形等优点而在航空、航天结构上得到了广泛应用.但是,当前服役飞机结构中的主承力构件仍主要使用金属材料,这就不可避免地要对复合材料结构和金属构件进行连接.由于复合材料的各向异性和多模式损伤形式,其与金属的连接部位成为整个结构的薄弱部位.飞行器的复合材料G金属结 构 件 有 70% 以 上 的 破 坏 都 发 生 在 连 接 部位[1],因此,对复合材料和金属的连接性能进行研究具有重要的工程意义.
累积损伤有限元分析方法被广泛应用于复合材料结构的各种受载分析中.CHANG[2]、TAN[3G4]和SLEIGHT[5]等很早就应用累积损伤有限元分析方法对复合材料结构进行了损伤分析,分析结果与试验数据较吻合.此后,许多研究者在利用该方法对复合材料结构进行损伤分析和强度预测等方面均取得了很好的结果[6G10].累积损伤有限元分析方法主要包括应力分析、失效判定和材料性能退化准则[11G13],其主要采用的失效判定准则有最大应力准则[14]、Hashin准则[15]、Chang准则[16]和 Puck 准则[17]等.这些准则大多以应力作为参考值,这是因为在有限元算法中,单元损伤前后的应力变化比较剧烈,而应变变化比较平缓.目前,基于应变的失效判定准则研究较少,且在复合材料G金属连接结构方面的应用更少.因此,作者以某型飞机机身尾段典型连接结构(复合材料G金属连接结构)为研究对象,利用 ANSYS有限元软件建立了该连接结构的三维有限元模型,应用累积损伤分析方法对该连接结构进行了失效预测及破坏规律研究,并进行了试验验证,为该型结构在工程上的应用提供参考
1 试验方法与结果
1.1 试样制备与试验方法
试样取自飞机尾端与后机身连接部位,尺寸如图1所示.
试样由一块 LY12铝合金板和一块复合材料层合板通过两排钛合金抗剪型100°沉头高锁螺栓 YSA302G5G7A 和 高 锁 螺 母 YAS361G5 连 接.复合材料层合板由3238A 环氧树脂/CF3031碳纤维织物(简称3238A/CF3031)预浸料和3238A 环氧树脂/CCF300碳 纤 维 (简 称 3238A/CCF300)预 浸料按一定方式铺层后,在300 ℃固化3h 而得到.3238A/CF3031、3238A/CCF300预浸料的单层厚度分别为0.23,0.125mm,铺层方案为(±45)/(0/90)/0/(±45)2/0/(0/90)/(±45)/0/(±45)/0/(±45)/0/(±45)/0/(±45)/(0/90)/0/(±45)2/0/(0/90)/(±45).制备得到的复合材料层合板厚4.45 mm.LY12铝合金板的厚度为3mm,热处理状态为 T3.
按图1所示位置,在试样上粘贴 SDY2206静态电阻应变片,采用 MTS810型强度试验机进行室温静载拉伸试验.试样上下两端夹持,下端加载,加载速率为1kN??s-1,每次达到5kN的倍数时保载10s,随后继续加载.此外,在试样上加装了防弯夹具(如图2所示)后,在相同条件下再进行了室温静载拉伸试验.
1.2 试验结果与讨论
在静载拉伸时发现:当加载载荷达到67.4kN时,未加装防弯夹具试样发出脆响;当加载至75kN时,在连接螺栓处出现凸起;继续加载,试样发出连续的脆响,出现载荷降低现象,螺栓处凸起更加明显;当加载至79.6kN 时,试样从连接处脱开.加装防弯夹具试样在加载至69.2kN 时发出脆响,复合材料层合板的部分接头处出现损伤,但载荷无降低现象;加载至80kN 时,试样出现连续响声;加载至84.8kN 时,听到 巨 大 脆 响,试 样 从 连 接 处 完 全 脱开,载荷迅速回落.由图3(a)可以看出,未加装防弯夹具的试样在拉伸破坏后出现了明显的弯曲现象.这是因为铝合金和复合材料的厚度不同,拉伸时载荷在螺栓连接处产生了较大的弯矩,导致试样发生弯曲.而在实际结构中,连接部位通常有桁条或壁板支持,抗弯能力较强,因此,为得到该结构的实际拉伸破坏载荷,试样需要加装防弯夹具.由图3(b)可见:加装防弯夹具拉伸后,试样中的复合材料表现为局部的粉碎性破坏,从接头螺栓安装孔位置沿螺栓挤压方向至复合材料板端部被完全破坏;破坏位置可见纤维断裂和纤维拔出现象,而分层现象则主要出现在螺栓孔部位两侧的区域内.这说明在整个加载过程中,试样基体局部以及连接界面发生了严重的破坏.无防弯夹具时,破坏模式为拉脱破坏,试样发生明显弯曲;加装防弯夹具后,试样发生挤压破坏.取90°方向的应变片,即图1中应变片3,6,9,12,15,18的应变值作载荷G应变曲线.由图4可以看出:在拉伸初始阶段,试样的应变随载荷的增加呈线性变化,应变变化比较均匀;各测点的应变变化趋势相同,铝合金板上的应变(即应变片12,15,18测得的应变)高于复合材料上的(即应变片3,6,9测得的应变);当加载至70kN 左右时,应变随载荷的增大呈非线性变化,推测是因为连接结构内部出现了局部损伤,损伤扩展对应变产生了影响.
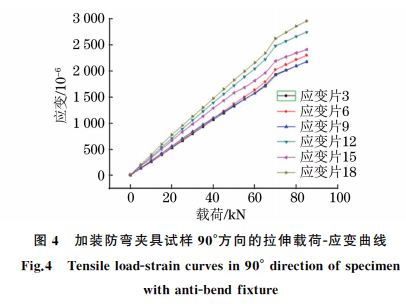
由表1可以看出,加装防弯夹具后,试样试验数据的分散性很小,且破坏载荷相对无防弯夹具试样的有所 增 大. 加 装 防 弯 夹 具 后 的 试 验 结 果 更 加准确.
2 有限元建模与分析
2.1 有限元模型
在 ANSYS有限元软件中建模,采用8节点三维层状体单元SOLID46模拟复合材料层合板,用8节点体单元SOLID45模拟铝合金板与高锁螺栓.为准确得到螺栓孔周边的应力、应变分布,对网格进行局部细化.假设高锁螺栓与复合材料层合板、铝合金板接头连接孔为无间隙配合,复合材料G金属连接结构中的螺栓孔壁受高锁螺栓挤压发生变形,同时螺栓受到拉伸载荷和剪切载荷作用发生变形.为合理模拟高度非线性的接触行为,采用 ANSYS软件中面G面接触单元 TARGET170和 CONTA174来定义接触对.为模拟试验中防弯夹具的效果,在模型外表面设置了垂直于表面方向的位移约束.复合材料G金属连接结构三维有限元计算模型如图5所示.
2.2 失效准则
由于有限元模型单元失效前后的应力变化剧烈,而应变变化相对平缓,因此为了正确判断复合材料G金属连接结构在拉伸过程中的主要损伤模式(基体破坏、纤维断裂和分层失效),在其累积损伤模型中,采用 Hashin准则和 Ye分层准则[18]作为复合材料失效判据,根据应力G应变关系,将基于应力描述的失效准则转换为基于应变描述的失效准则,进行失效预测分析.
假定复合材料单层的弹性常数不受层合板中相邻层的影响,则单层材料主方向的应力G应变关系为
式中:σ为拉伸强度;τ为剪切强度;ε为拉伸应变;γ为剪切应变;下标1,2,3分别代表纤维轴向、纤维横向和单层板法向;Cij 为刚度系数.通过式(1)推 导 建 立 基 于 应 变 描 述 的 失 效 准则,纤维拉伸失效(ε1 >0)、纤维压缩失效(ε1 <0)、基体拉伸或剪切失效(ε2 >0)、基体压缩或剪切失效(ε2 <0)和分层失效准则分别为
式中:ε11,ε22和ε33 分别为1,2,3方向的应变,上标T 和 C分别表示拉伸和压缩;γ012,γ013 和γ023 分别为对应于剪切强度τ12,τ13和τ23的剪切应变.
2.3 材料性能退化准则
在复合材料层合板承受外加载荷时,当其结构内部单元的应力、应变满足式(2)~式(6)之一时,可认为这些单元失效,需要对失效单元的材料性能进行退化处理.对于损伤过程中的材料性能退化,研究人员提出了多种退化模型[19G21].作者对其中的Camanho损伤退化模型进行了改进,得到的材料性能退化准则的具体描述如下:
(1)纤维拉伸失效时,假设该失效单元不能承受任何载荷,E1,G12,G13,ν12,ν13 退化为初始值的1%,E2,E3,G23,ν23退化为初始值的6%(E 为弹性模量,G 为剪切模量,ν为泊松比).
(2)纤维压缩失效时,假设该失效单元不能承受任何载荷,E1,G12,G13,ν12,ν13 退化为初始值的2%,E2,E3,G23,ν23退化为初始值的12%.
(3)基体拉伸或剪切失效时,E2,ν12 退化为初始值的1%,G12,G23,ν23退化为初始值的10%.
(4)基体压缩或剪切失效时,E2,ν12 退化为初始值的2%,G12,G23,ν23退化为初始值的20%.
(5)分层失效时,E3,G13,G23,ν13,ν23退化为初始值的2%.实际上,损伤机理具有相互关联性,一种类型的损伤可能诱发其他类型的损伤.对于包含多种损伤类型的局部损伤区域,应采用相应损伤类型的材料退化方式进行叠加.
2.4 累积损伤
由图6可以看出:当静拉伸载荷增至65kN 时,复合材料层合板与金属连接处出现明显损伤,即初始破坏载荷为65kN,损伤从复合材料层合板接头螺栓安装孔受挤压区域产生;初始破坏载荷模拟值与静拉伸试验结果(68.3kN)相近,相对误差仅为4.8%;随着载荷的增大,复合材料层合板的损伤逐渐累积,并主要沿螺栓挤压方向扩展;当载荷增至75kN 后,损伤迅速扩展,失效单元数量大大增加;当载荷达到90kN时,复合材料层合板的损伤区域扩展至其与金属连接的端部,导致该复合材料G金属结构连接件失去承载能力,即最终破坏载荷为90kN,模拟结果高于静拉伸试验测试结果(84.5kN),相对误差为6.5%.对比图6和图3(b)可知,模拟得到的复合材料层合板损伤部位与试验结果吻合较好.
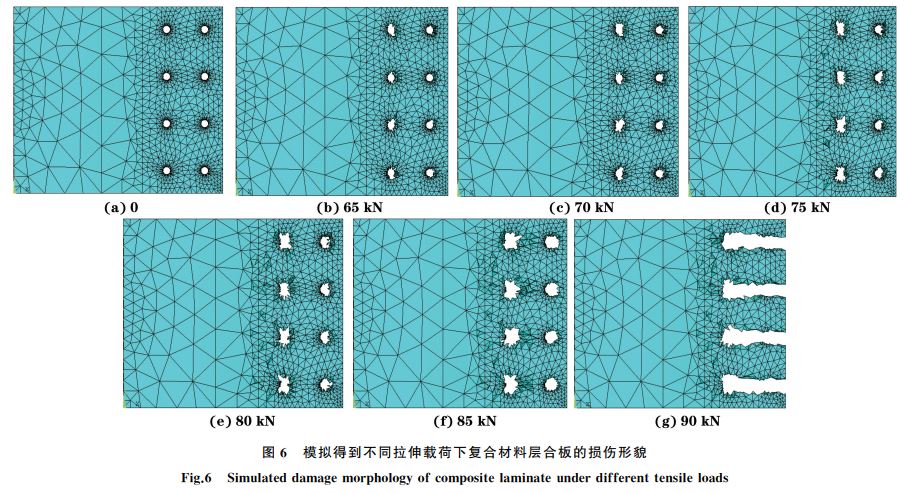
3 结 论
(1)复合材料G金属连接结构件试样在加装防弯夹具后,其平均拉伸破坏载荷由未加装防弯夹具
的79.6kN 增加到84.5kN,拉伸破坏模式由拉脱破坏变为挤压破坏.
(2)加装防弯夹具后,复合材料G金属连接结构件试样在较小的拉伸载荷下,其应变随载荷的增加呈线性增大,当拉伸载荷大于70kN 后,应变与载荷呈非线性变化;在金属上的应变明显大于复合材料层合板上的.
(3)模拟得到复合材料G金属连接结构件的初始破坏载荷为65kN,与静拉伸试验得到的68.3kN接近,相对误差为4.8%;最终破坏载荷为90kN,与拉伸试验值的相对误差为6.5%;损伤从复合材料层合板接头螺栓安装孔受挤压区域产生,随着载荷的增加而逐渐累积,并主要沿螺栓挤压方向扩展,连接结构件出现挤压破坏,与试验结果相符.该复合
材料G金属连接结构三维有限元累积损伤模型能够有效预测复合材料G金属连接结构件的损伤扩展过程及破坏模式.